GALVANIZING
Galvanizing
Sureway Galvanizing offers hot dip galvanizing to meet all your commercial and industrial needs. Our facility is equipped with state-of-the-art equipment to ensure a quality product with a fast turnaround. We utilize the latest galvanizing techniques so that your products are given extended protection from corrosion and other adverse conditions.We understand that trust is key to any partnership. With our knowledgeable and experienced staff, we will guide you through the entire process. From the initial design phase to determining the right galvanizing process, you can rest assured that your project will be completed on time and to the highest possible quality.
Not only does galvanizing protect your steel, it also adds to its aesthetics. The zinc layer adds a smooth, shiny finish, perfect for products that require a more professional and quality look.
Contact Sureway today for a galvanizing quote and get the most out of your steel investments. galvanizing@surewaymetal.com
Galvanizing is Green - View PDF
Galvanizing for Sustainable Design - View PDF
Hot-dip galvanizing is a metallurgical bond between steel and molten zinc, produced in specific installations and under controlled conditions. The process of molecular bonding between two metals is unique and simple yet provides excellent molecular bonding and cathodic protection.
Please note that, to maintain our process' efficiency and optimal performance, we regularly inspect all process solutions and equipment, as well as our procedures and measuring (and verification) equipment.
Galvanizing for Sustainable Design - View PDF
What is Hot Dip Galvanizing?
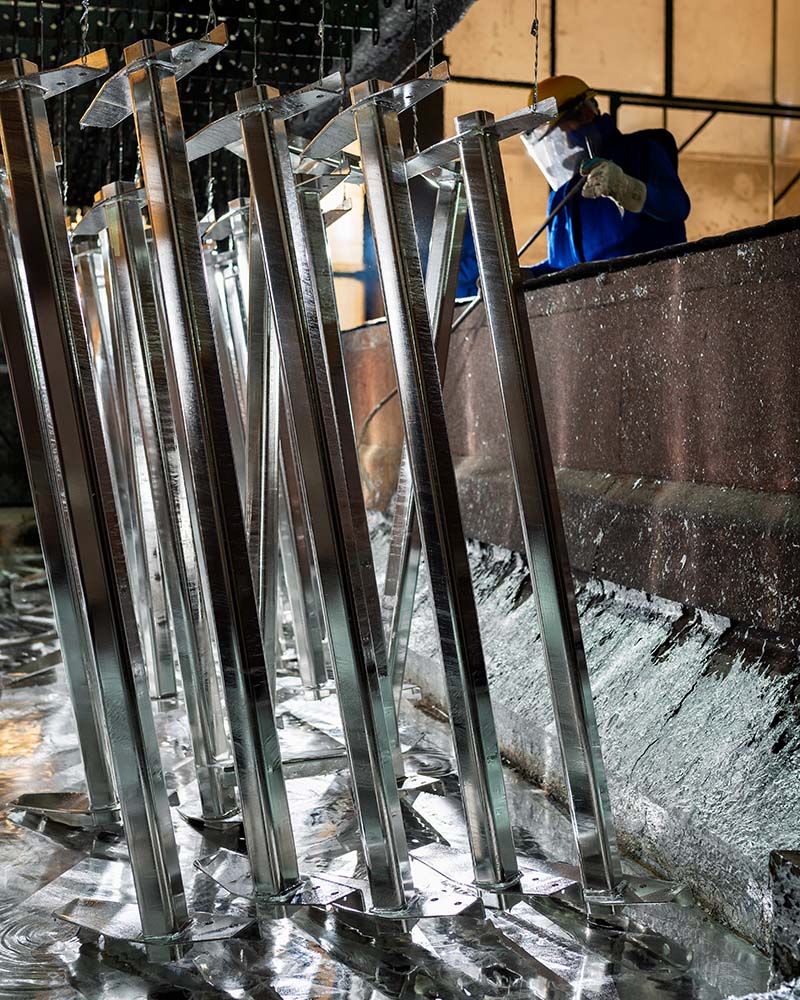
Pre-galvanizing inspection of materials
We will begin by inspecting all received material to ensure that the steel can be galvanized according to specifications and to determine if:- Design, welds, fabrication methods and general surface conditions are allowing for regular HDG-steps and process.
- There is paint or any other contaminant (varnish, lacquer, etc.) that requires additional steps, such as cleaning by sandblasting or chemical treatment.
- Steel assemblies require extra draining and venting holes.
- There is indication of other elements potentially affecting the normal galvanization process.
Cleaning and grease removal
The steel is then processed for surface preparation:- Grease, oil, markings, and dirt removal in a degreasing solution.
- Pickling hydrochloric or sulfuric acid solutions remove all traces of surface rust and mill scale.
Fluxing
When the steel is thoroughly cleansed, it is then immersed in a liquid flux - ammonium chloride solution - that will protect and prevent oxidation prior to dipping in the molten zinc bath. It will also promote the steel's adhesive properties.Galvanizing
- Once surface preparation is complete, the steel is immersed in a bath of molten zinc at between 815-850F. During this step, the zinc metallurgically bonds to the steel, creating a series of highly abrasion-resistant zinc-iron alloy layers, commonly topped by a layer of impact-resistant pure zinc.
- This step requires very little time, and the zinc alloy layers are created when the steel reaches the temperature of the molten zinc. Once the layers are formed, the material is slowly withdrawn from the kettle, which usually provides a smooth and uniform surface.
Cooling / Quenching
- Upon exiting the zinc kettle, excess zinc is removed by draining and cooled by dipping in water (commonly called quenching), allowing quick handling.
- Other cooling solutions exist - they contain other substances allowing for partial passivation of surfaces, which in turn prevent staining and premature oxidation. In the case of reinforcing steel (or rebar), it is preferable to use a chromate solution: this substance promotes compatibility with various concrete compounds.
- In some cases, quenching might not be recommended because of design considerations or because of the products end-use. Air-cooling is then recommended. Circumstances and practices can include distortion prevention and painting after galvanizing.
Final inspection
Surface condition and coating thickness inspections complete the process. They will ensure that the galvanizing meets international hot-dip galvanizing standards. A certificate of conformity is available upon request.Please note that, to maintain our process' efficiency and optimal performance, we regularly inspect all process solutions and equipment, as well as our procedures and measuring (and verification) equipment.
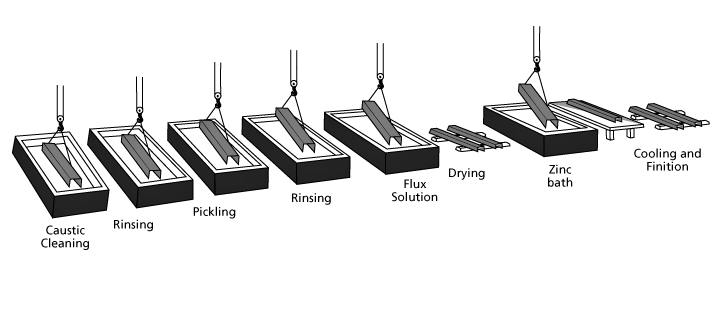